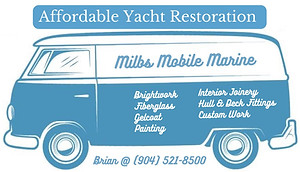
9610 Commonwealth Ave., Jacksonville, FL 32220
9) CD 27 - G-10 Backing Plate Test Fit & Base Layer of 1708
February 3, 2024
The previous evening, I prepared the backstay knees for the lazarette locker (to support and transfer load from the backstay), and also fabricated the two backing plates to support the port and starboard sidestays and shrouds. I set off immediately to finish up a bit of surface prep (sanding), using the Makita 9031 finger belt sander - in a previous session the belt finally failed, calling to a stop the small amount of surface prep remaining. With that small amount of prep complete, I moved onto the deck of the Cape Dory 27, and using a small palm sander, removed the factory finish from the new G-10 backing plates. I rounded over the edges, and then headed back into the salon for a test fit. As can be seen, and with a bit of finesse, I managed to place the new backing plates in position with good success. These plates would be glued to the underside of the hull/deck flange, glassed from backing plate to roughly 16" down the interior side of the hull, and finally, through-bolted from the deck padeyes.
I removed the backing plates and set them to the side, and turned my attention to cleaning up the sanded surfaces of the hull and hull/deck flange for what I am calling a "tie" layer of 1708 biaxial cloth. The initial layer would cover as much surface area as the space allowed (head and hanging locker access, as well as the cutout liner in the salon). Next would be backing plates and then a schedule of 1708 biaxial cloth to unify the backing hull/deck flange, backing plate, and hull - allowing good support and load transfer from the rig.
I vacuumed and wiped all surfaces with acetone to remove surface contaminates and sanding detritus. Next, I used a lightweight kraft paper to template the hull surfaces - two on the port, and two on the starboard side. The templates were then used to prepare a "tie" layer of 1708 biaxial, as well as a layer of peel play to cover the fiberglass through the curing process. Using the peel ply would reduce required sanding, helping to keep the interior as clean as possible. All fiberglass and peel ply was cut and set to the side. I then applied "neat" epoxy to all surfaces to be glassed, followed by thickened epoxy to fill in some of the more egregious gouges and voids.
The fiberglass itself was wet out with epoxy, rolled up, and then unrolled onto the hull surface, working from the bottom up. I worked the cloth to align it and to remove air bubbles, and then followed on with the peel ply. That would wrap up the session, and I gathered tools and straightened up Doryen for the next visit.
Total Hrs: 5.5